- Reduction of transport kilometers: 5%.
- Savings in process costs: 80%
Powered by
x
Fallstudie
Dynamic route planning at the push of a button
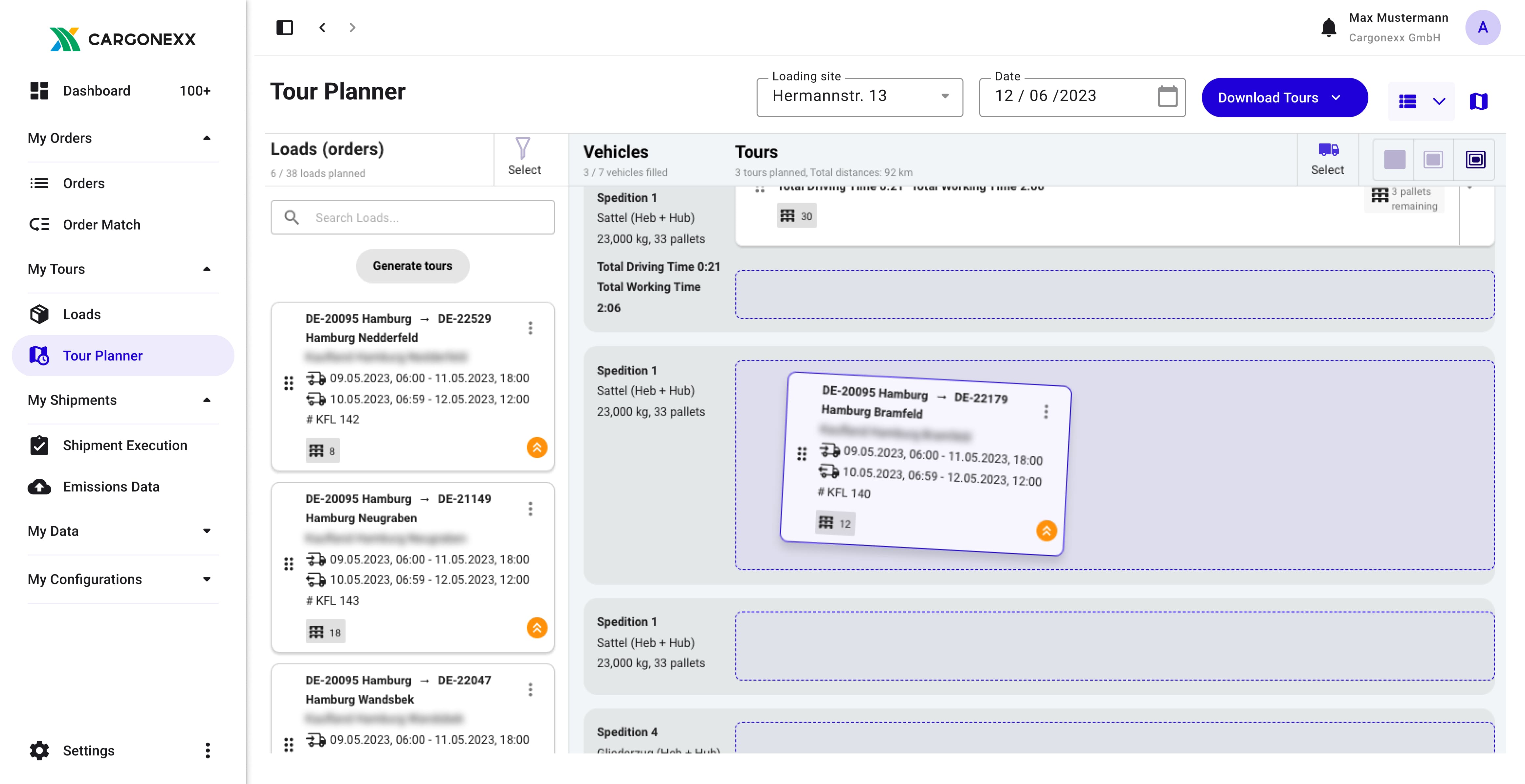
A manufacturer of soft drinks wants to digitize its processes in the company. The goal: to continue to work in a contemporary manner and to provide employees with the latest software solutions. Management expectations: Processes should be made visible, thus reducing transport and process costs and creating process reliability in logistics.
With automated route planning, Cargonexx enables fast and flexible planning of orders on a daily basis. In doing so, we place particular emphasis on the dispatcher's way of working and allow interventions in the planning at any time. Planned tours that cannot be realized due to daily complications or customer-specific restrictions can be prioritized.
Get your free demo.